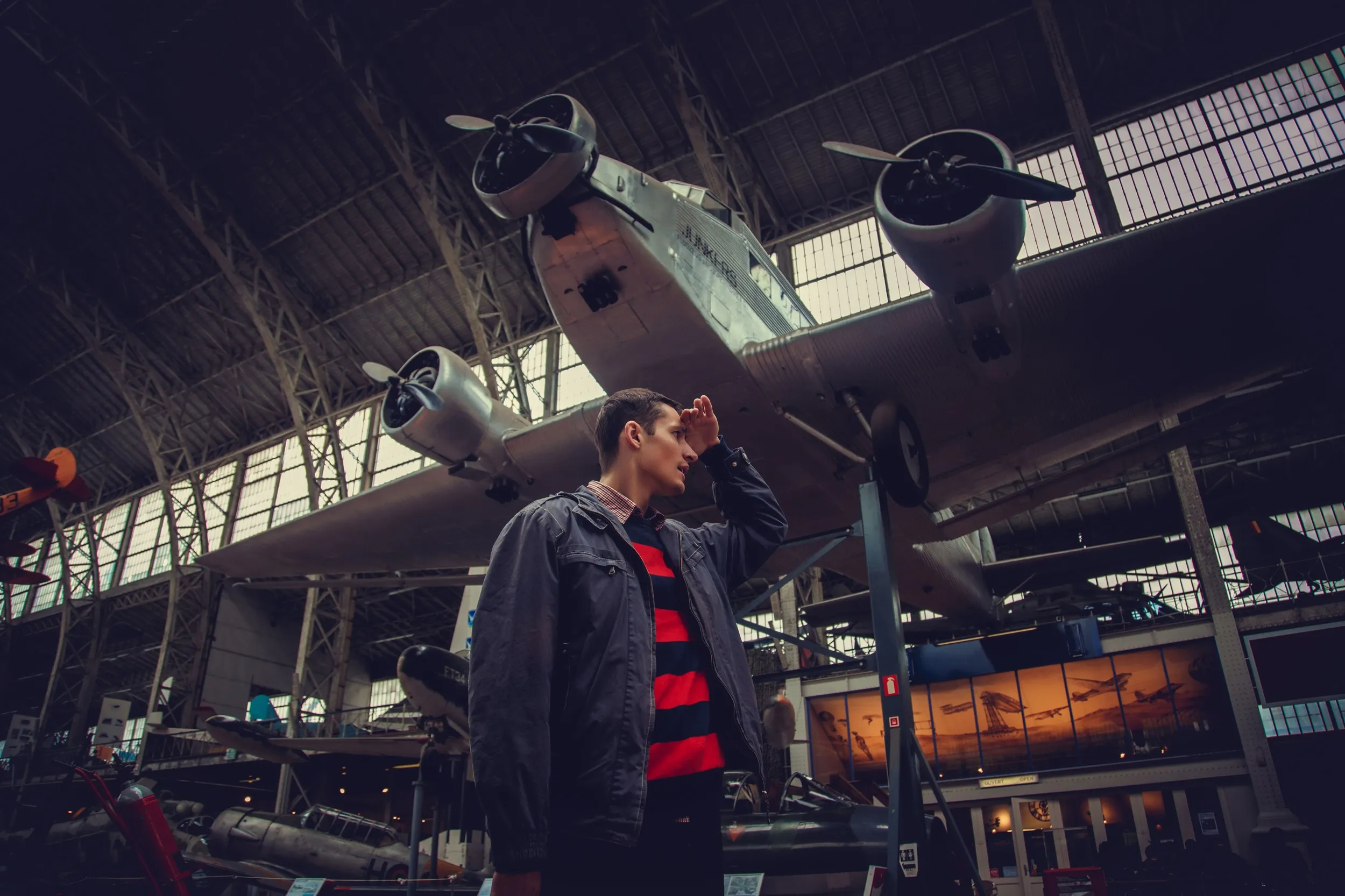
Introduction
In the aerospace industry, every ounce of flying weight counts. Reducing the weight of aircraft components without compromising strength and performance is crucial for improving fuel efficiency, reducing emissions, and increasing payload capacity. Ultra-precise machining techniques have revolutionized the way manufacturers achieve these weight savings, enabling the production of lighter, stronger, and more efficient aircraft.
Current trends of machining single piece, monolithic components leverages the latest state of the art in machine tools to further consolidate weight savings, reduce assembly issues and increase reliability. At Green Wing Partners, we specialize in leveraging cutting-edge machining technologies to achieve unparalleled weight savings, setting new standards in the industry.
The Importance of Weight Savings in Aerospace
Weight reduction is a key driver in aerospace manufacturing due to its significant impact on fuel efficiency and overall performance. Every pound saved translates into lower fuel consumption, reduced operating costs, and a smaller carbon footprint. As the industry continues to prioritize sustainability, the demand for innovative weight-saving solutions has never been higher.
Ultra-Precise Machining: The Game Changer
Ultra-precise machining leverages advanced CNC (Computer Numerical Control) machine tools and unique techniques to produce components with exceptional accuracy and minimal material waste. This new, higher level of precision allows manufacturers to maintain the component, the vacuum fixture and the machine tool frame itself all with a few degrees of standard temperature & pressure (STP) no matter how large the machine frame is. Ultra large gantry machine tools designed to machine multiple identical wing skins simultaneously can be as large as 30 feet wide by 200 feet long. Gantry machine tools up to this size are typically housed inside of a non-air conditioned facility.
This is especially important when dry machining [zero liquid for cutter lubrication or cooling] aluminum wing skins for the commercial aircraft industry As is currently accepted, the wing skin is dry machined with a typical cycle time of up to 8 hours. Most but not all of the “heat in the cut” from dry machining is typically absorbed into the chips which are vacuumed away as fast as they are created. However, the left over or residual heat will be absorbed into the wing skin causing various defects in the skin such that the skin fails final inspection. By maintaining wing skins within a few degrees of the ideal STP, the usual and customary typical bowing, warping, and blistering on the very thinnest areas near the edges and near the wing tip are prevented from occurring.
Maintaining skins, vacuum fixturing and the machine tool frame very close to the ideal STP conditions reduces many temperature coefficient of expansion driven issues to practically zero.
Key Techniques in Ultra-Precise Machining
- High-Speed Machining (HSM): High-speed machining involves using higher spindle speeds and feed rates to remove material more efficiently. This technique not only reduces machining time but also improves surface finish and dimensional accuracy, resulting in lighter components with superior performance.
- 5-Axis Machining: Unlike traditional 3-axis machines, 5-axis machining allows for the simultaneous movement of the cutting tool along five different axes. This capability enables the production of complex geometries and intricate designs with greater precision, reducing the need for additional fixtures and material.
Benefits of Ultra-Precise Machining
- Material Efficiency: Ultra-precise machining minimizes material waste by ensuring that only the necessary amount of material is removed. This efficiency translates into lighter components and reduced material costs.
- Enhanced Performance: Components manufactured with ultra-precise machining exhibit improved strength-to-weight ratios, contributing to overall aircraft performance and reliability.
- Consistency and Repeatability: The high level of accuracy achieved through ultra-precise machining ensures that each component meets exact specifications, resulting in consistent quality across production runs.
- Design Flexibility: Advanced machining techniques allow for the creation of complex geometries and lightweight designs that were previously unattainable, enabling engineers to push the boundaries of innovation.
Advanced Techniques for Greater Efficiency
The implementation of advanced techniques such as high-speed machining and 5-axis machining significantly enhances manufacturing efficiency. High-speed machining reduces the time required for material removal, thus accelerating production timelines without compromising precision. This is particularly beneficial for producing complex geometries, which demand a higher degree of accuracy and intricacy.
5-axis machining, on the other hand, offers an unprecedented level of flexibility in handling intricate designs and complex angles. The simultaneous movement along five different axes reduces the need for multiple setups and manual adjustments, leading to shorter production cycles and reduced labor costs. By integrating these advanced techniques, Green Wing Partners can manufacture lighter components with a high degree of precision, ultimately contributing to significant weight savings and enhanced aircraft performance.
Adapting to Evolving Industry Demands
As the aerospace industry evolves, the demand for lighter, more efficient components continues to rise. The emphasis on fuel efficiency, environmental sustainability, and cost-effectiveness drives manufacturers to adopt innovative machining techniques that deliver substantial weight savings. Ultra-precise machining not only meets these demands but also sets new benchmarks for quality and performance.
Environmental Impact and Sustainability
The environmental benefits of weight reduction in aircraft are profound. Lighter aircraft consume less fuel, resulting in lower carbon emissions and reduced environmental impact. By adopting ultra-precise machining techniques, manufacturers can contribute to sustainability goals and support the industry's efforts to minimize its carbon footprint. Green Wing Partners is committed to implementing eco-friendly practices that align with global sustainability initiatives, ensuring that our manufacturing processes contribute positively to the environment.
Case Study: Achieving Weight Savings with Ultra-Precise Machining
At Green Wing Partners, we recently collaborated with a leading aerospace manufacturer to develop a new series of aircraft components with significant weight savings. By employing high-speed machining and 5-axis techniques, we were able to reduce the weight of critical structural components by up to 20%. These components not only met but exceeded the stringent performance requirements, showcasing the potential of ultra-precise machining in revolutionizing aerospace manufacturing.
Innovations Driving Future Success
The continuous advancements in machining technology pave the way for even greater achievements in weight reduction and precision manufacturing. Innovations such as additive manufacturing, artificial intelligence, and machine learning are poised to further enhance the capabilities of ultra-precise machining. By staying at the forefront of these technological developments, Green Wing Partners is dedicated to delivering cutting-edge solutions that drive the future of aerospace manufacturing.
Partner with Green Wing Partners for Precision and Performance
At Green Wing Partners, we are dedicated to pushing the boundaries of precision manufacturing to achieve remarkable weight savings in aerospace components. Our state-of-the-art machining technologies and expert team ensure that every part we produce meets the highest standards of accuracy and performance. If you’re looking to enhance the efficiency and sustainability of your aircraft, partner with us for cutting-edge solutions that deliver unmatched results.
Conclusion
Ultra-precise machining techniques have transformed the landscape of aerospace manufacturing, enabling significant weight savings and improved performance. As the industry continues to evolve, the demand for precision and efficiency will only grow. Green Wing Partners is at the forefront of this movement, leveraging advanced machining technologies to create lighter, stronger, and more efficient aircraft components. By embracing these innovations, we can drive the future of aerospace toward greater sustainability and success.