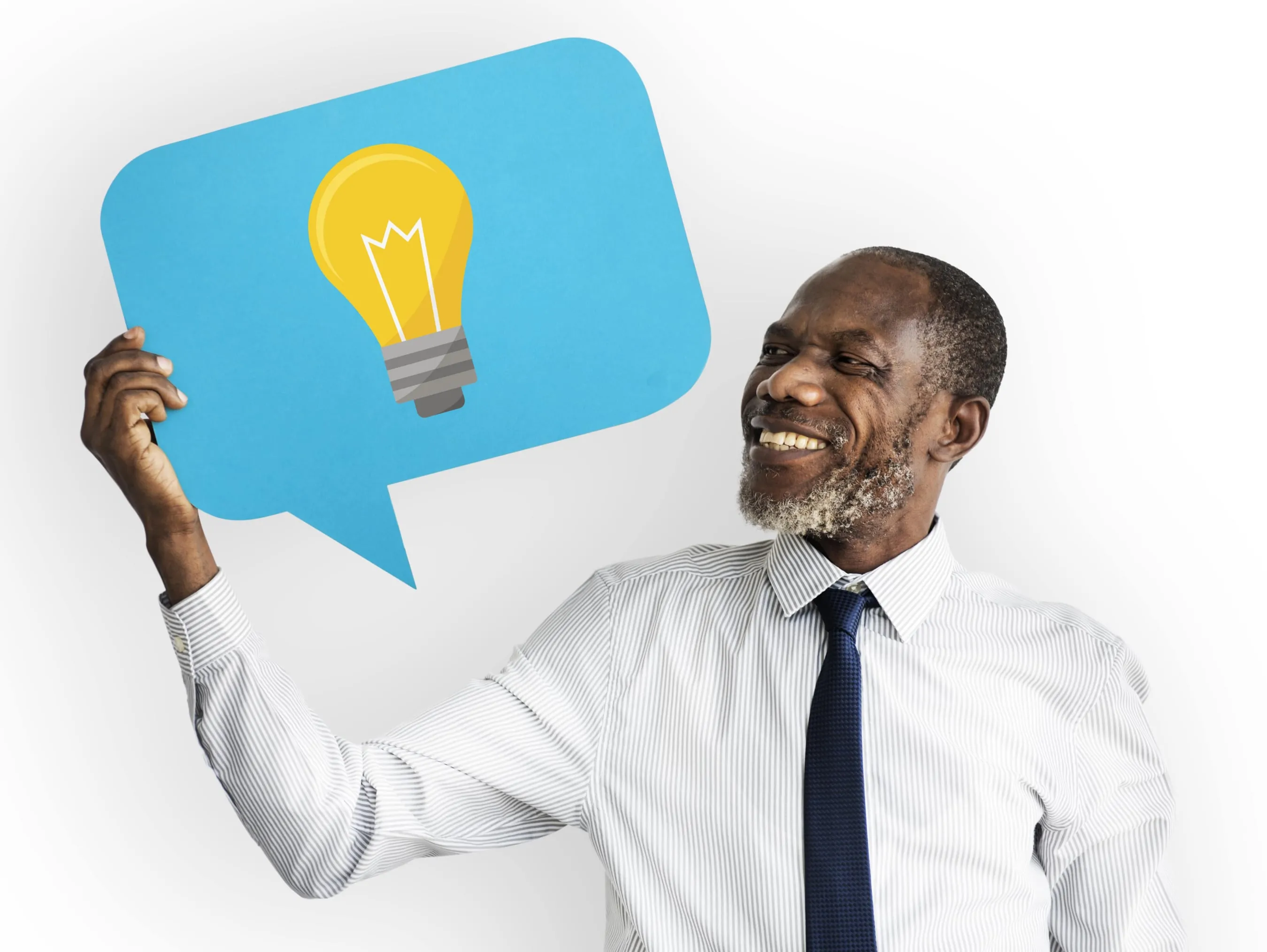
When I worked at Boeing, I was a CNC Maintenance Tech. One day, after a brief safety meeting, I was riding my work tricycle out to the gantry mill when I heard a loud noise coming from a different gantry machine nearby. The noise was deafening, so I put on earplugs and earmuffs. As I walked up, I saw a very small part, estimated to be about 45 feet long and 3 feet wide, attached at the bottom much like you would hold a tuning fork from the bottom.
This part was vibrating so intensely that it was shaking the fixture holding the part, the machine frame, and even the 8 feet wide, 8 feet deep, and 75 feet long concrete foundation. Standing about 10 feet away from the machine base, I could feel the vibrations through the soles of my feet despite my heavy work boots and two sets of insoles. This was the worst machining I had ever witnessed. I thought to myself, there must be a better way. I finished both of my shifts that weekend.
The following Monday morning, while reading through the latest issue of “Tooling and Production,” I came across an article about polymer-enhanced concrete and its vibration damping attributes. In that eureka moment, I realized I had almost all the basic skill sets needed to design, engineer, fabricate, test, and finish machine a vacuum fixture base plate to hold the wing part at work.
My father was a carpenter, and I had helped him pour concrete in various projects on the farm growing up. Having commissioned very large vacuum heat treat furnaces, I knew how to design for vacuum. I designed in large diameter piping for highly efficient vacuum pumping. I could fabricate precise engineered wood forms to tight tolerances for casting on a simple but accurate table saw. I also designed the matching aluminum cooling plate with integrated vacuum ports and the rubber vacuum seal groove design for optimum effect. Additionally, I had experience precisely bending tubing from my days working in construction.
The only part I was missing was an optimal concrete mix to greatly increase stiffness, 4.5 times compressive strength, and essentially zero natural porosity, designed to resist heat flow and match the thermal coefficient of expansion (TCE) of steel. I began researching standard admixtures and mix design, reaching out to a few concrete engineers for guidance. With their help, I was offered samples of admixtures by the companies they worked for.
Working in my double garage with a small concrete mixer, a standard carpenter’s table saw, and many hand tools, I adopted a systematic “design of experiments” approach to create and optimize my mix designs. I started creating 24” by 2” by 4” ingot samples for testing and incorporated post-tensioning for extra added strength. Within six months, I could pour any shape I desired with embedded steel threaded inserts for bolting into or through my castings. Initially, I extended the “ways” (aka linear guides) of my Bridgeport knee mill and created two standalone grinder bases, allowing me to machine and grind bigger, longer parts as the moveable axis now traveled twice as far.
When that worked, I bought a much bigger scrap cast iron, 16 feet long, 6000-pound casting for a song and started by adding rollerball linear guides along with a rack and pinion drive for motion. The new X axis was a double offset, two layers of 1” thick steel plates which I machined by hand, hanging off a small steel gantry hoist on top of my newly enhanced Bridgeport knee mill in the garage. The plates were annealed, straight ground, and bolted together to slide upon the dual linear guide bearings on the 16’casting. The 16’ casting with a horizontal axis casting was mounted on top of a custom poured, high-strength, and post-tensioned concrete casting 24” high by48” wide and 20’ long, which I poured myself. I used an old, $100 forklift and a used 3-ton rated engine hoist to lift the casting up on top of the 24-inchhigh concrete foundation with the help of two assistants.
I hired a local Computer Aided Design (CAD) young man whose dad owned a machine shop nearby for about three months. I sketched out portions of the rest of the machine design and did all the force and moment calculations on the fly. He drafted it up in CAD, providing accurate dimensions for all parts, allowing me to saw, cut, drill, and bolt up the steel frame. I also designed and fabricated two complex 3-meter vertical columns which sat on two 8-foot-long polymer beams, holding the moveable Y and Z axis perpendicular to the 16’ long horizontal axis. I mounted the new temperature-controlled vacuum fixture on this assembly.
Once the milling machine was assembled, aligned, and the controls moved the motors, it was time to test the machine. We started with tooling foam, which is hard enough to replicate the cut surfaces exactly. After measuring the cut features to verify the mill's accuracy, we used laser compensation for 99% inaccuracy in all axes, followed by re-cutting foam to confirm the laser compensation values. Then we machined a soft material like aluminum to check rigidity and repeatability, achieving ± 0.0012” accuracy over10 feet in X, Y, and Z axes.
We initially used a scrap aluminum plate, 24” by 24”by 1” thick, milling one large pocket 22” by 22” by .940” deep for a very thin layer left on the bottom. We then milled a 48” by 48” by 1” thick scrap plate with a pocket of 44” by 44” by .940” deep multiple times, achieving a thin0.060” face left over, which was straight and not warped, proving the process repeatability.
The thinner the material, the easier it is to warp, twist, and bow, making the 0.060” plate a worst-case scenario. Using soft tap water measured at 52°F to 54°F and 38 psi pressure for cooling, we achieved a flow rate of 0.61 gallons per minute, maintaining the fixture cool to the touch even on a 75-80°F summer day.