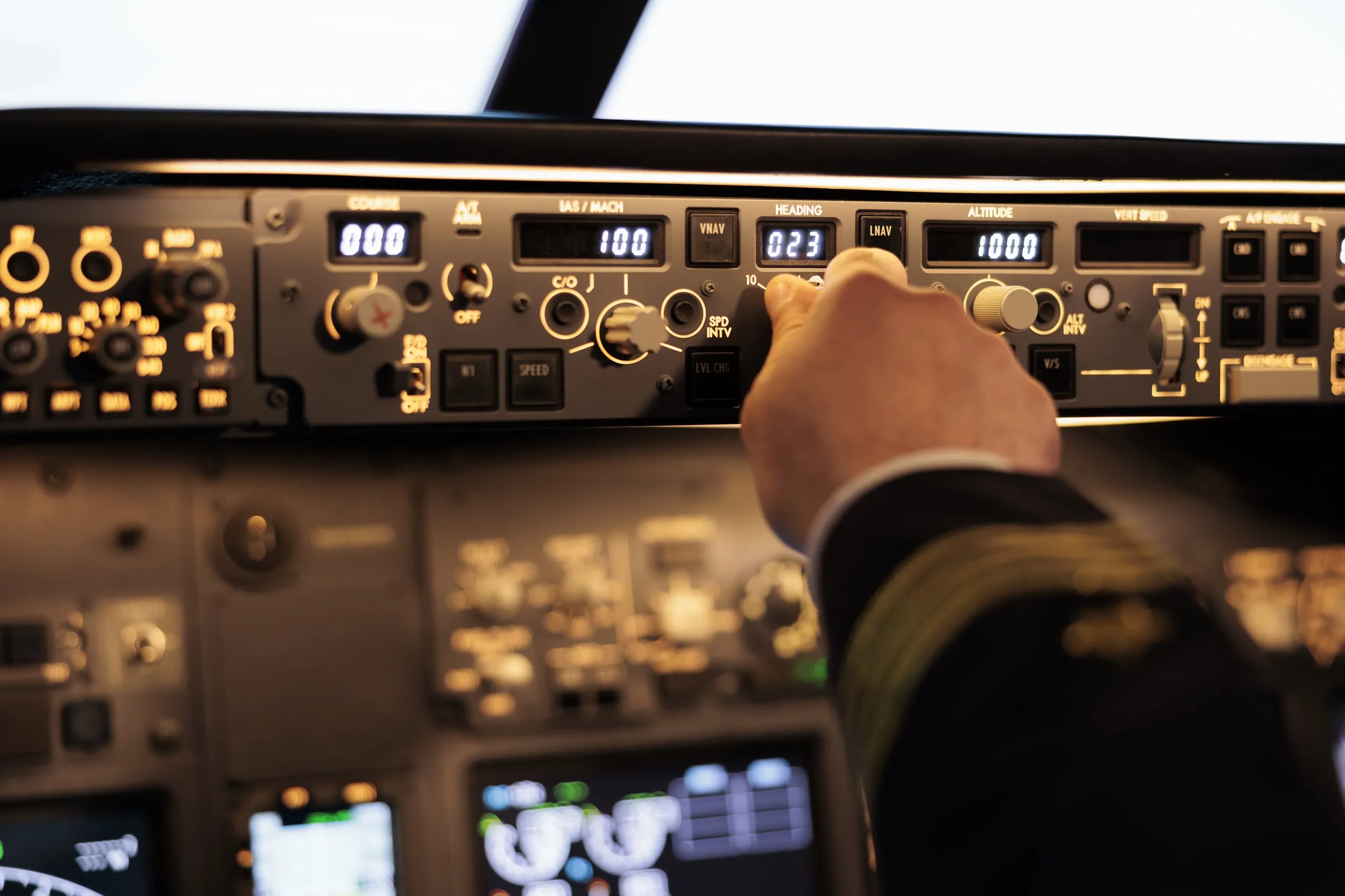
Introduction
In the aerospace manufacturing industry, maintaining precision and accuracy in machining processes is essential. However, certain scenarios necessitate a more pragmatic approach, where designing in excess manufacturing tolerance can compensate for low accuracy machining. This strategy ensures the reliability and functionality of components while streamlining production processes, reducing costs, and achieving significant weight savings. At Green Wing Partners, we specialize in optimizing manufacturing tolerance to meet the demands of aerospace engineering, offering innovative solutions that balance precision with practicality and environmental benefits.
Understanding Manufacturing Tolerance
Manufacturing tolerance refers to the permissible limits of variation in a physical dimension or measured value. In the context of machining, it defines the acceptable range within which a component's dimensions can vary without compromising its performance. Tight tolerances require high precision and accuracy, often leading to increased production costs and complexity. Conversely, excess tolerance allows for more flexibility in the machining process, making it a viable solution for certain applications, particularly when considering weight savings and light weighting.
The Role of Excess Manufacturing Tolerance
Excess manufacturing tolerance involves intentionally designing components with greater allowable variation in dimensions. This approach is particularly beneficial in scenarios where high precision is not critical, or where low accuracy machining processes are employed. By accommodating a wider range of dimensional variation, manufacturers can reduce the need for stringent quality control measures, lower production costs, improve overall efficiency, and achieve significant weight reductions.
Advantages of Excess Tolerance Design
- Cost Reduction: Designing in excess tolerance can significantly reduce production costs by minimizing the need for high-precision machining equipment and processes. This approach allows manufacturers to use more cost-effective methods without compromising the functionality of the final product.
- Improved Production Speed: Excess tolerance design enables faster production cycles by reducing the time required for meticulous quality checks and adjustments. This efficiency is particularly valuable in high-volume manufacturing environments where speed is a priority.
- Flexibility in Material Selection: By allowing for greater dimensional variation, excess tolerance design offers more flexibility in material selection. Manufacturers can choose materials that are easier to machine or more cost-effective, further reducing production expenses.
- Simplified Quality Control: With excess tolerance, the need for rigorous quality control is diminished. This simplification leads to fewer rejected parts, reduced rework, and streamlined quality assurance processes.
- Environmental Benefits: Designing for weight savings through excess tolerance can lead to significant reductions in CO2 emissions over the lifecycle of an aircraft. This aligns with the growing emphasis on sustainability in the aerospace industry.
Weight Savings and CO2 Emissions
A critical consideration in excess tolerance design is the potential for significant weight savings. For instance, the average wing skin of an aircraft has approximately 650 square feet of surface area. Due to nominal variations and environmental factors, manufacturers often leave an intentional excess material thickness of about 0.012 to 0.015 inches in the CAD model used to drive the machining tool path. This excess material ensures that the skin is not machined too thin, which would result in rejection.
To put this into perspective, every 0.001 inch of extra material left on the wing skin equates to almost 1.0 kilogram of weight. With an intentional manufacturing tolerance of 0.015 inches, up to 80% or 0.012 inches of excess material can be removed. Removing this excess material would reduce the weight of the skin by approximately 12 kilograms. Given that there are four skins per aircraft, this results in a total weight reduction of up to 48 kilograms or 105.6 pounds. This lower weight translates to reduced fuel consumption and lower CO2 emissions over the aircraft's 20+ year lifespan.
Challenges and Considerations
While excess manufacturing tolerance offers numerous benefits, it is essential to carefully consider its implementation to avoid potential pitfalls:
- Performance Impact: Excessive tolerance can affect the performance and reliability of components. It is crucial to strike a balance between cost savings and maintaining the necessary performance standards.
- Interchangeability: In assemblies where components must fit together precisely, excess tolerance can pose challenges. Ensuring interchangeability requires careful design and planning.
- Customer Requirements: Aerospace manufacturers must consider customer specifications and regulatory requirements. Any deviation from prescribed tolerances must be justified and communicated effectively.
Strategies for Implementing Excess Tolerance Design
- Functional Analysis: Conduct a thorough analysis of the component's functional requirements to determine where excess tolerance can be applied without compromising performance. Identify critical dimensions that require tight tolerances and those that can accommodate greater variation.
- Simulation and Testing: Utilize simulation tools and testing procedures to validate the impact of excess tolerance on component performance. This step ensures that the design meets the necessary standards while achieving cost and efficiency benefits.
- Collaborative Design Process: Engage in a collaborative design process involving engineers, machinists, and quality control experts. This interdisciplinary approach ensures that all aspects of the design are considered, leading to a balanced and effective tolerance strategy.
- Continuous Improvement: Implement a continuous improvement program to monitor the performance of components with excess tolerance. Gather feedback, analyze results, and refine the design as needed to optimize manufacturing processes.
Case Study: Enhancing Efficiency with Excess Tolerance Design
Green Wing Partners recently collaborated with an aerospace manufacturer to redesign a series of non-critical structural components using excess manufacturing tolerance. By identifying dimensions that could tolerate greater variation, we developed a new design that reduced production costs by 15%, increased production speed by 20%, and achieved significant weight savings. The redesigned components met all functional requirements and passed rigorous testing, demonstrating the effectiveness of excess tolerance design in achieving cost savings, efficiency, and environmental benefits.
Innovations Driving Future Success
The adoption of advanced technologies, such as machine learning and artificial intelligence, is further enhancing the capabilities of excess tolerance design. These innovations enable manufacturers to predict and compensate for dimensional variations more accurately, leading to even greater efficiency and precision in production processes. By staying at the forefront of these technological advancements, Green Wing Partners is committed to delivering cutting-edge solutions that drive the future of aerospace manufacturing.
Partner with Green Wing Partners for Innovative Manufacturing Solutions
At Green Wing Partners, we understand the challenges of balancing precision and efficiency in aerospace manufacturing. Our expertise in excess tolerance design and low accuracy machining allows us to develop cost-effective solutions that meet your specific requirements while achieving weight savings and reducing CO2 emissions. Partner with us to leverage our innovative approaches and achieve new levels of efficiency and performance in your manufacturing processes.
Conclusion
Designing in excess manufacturing tolerance offers a practical solution for compensating low accuracy machining, delivering significant cost savings, production efficiencies, and environmental benefits. By carefully implementing this strategy, aerospace manufacturers can achieve reliable, high-quality components while reducing production complexities. Green Wing Partners is dedicated to optimizing manufacturing processes through innovative tolerance design, ensuring that our clients benefit from the latest advancements in aerospace engineering. Embrace the future of efficient and sustainable manufacturing with Green Wing Partners, where precision meets practicality and environmental responsibility.