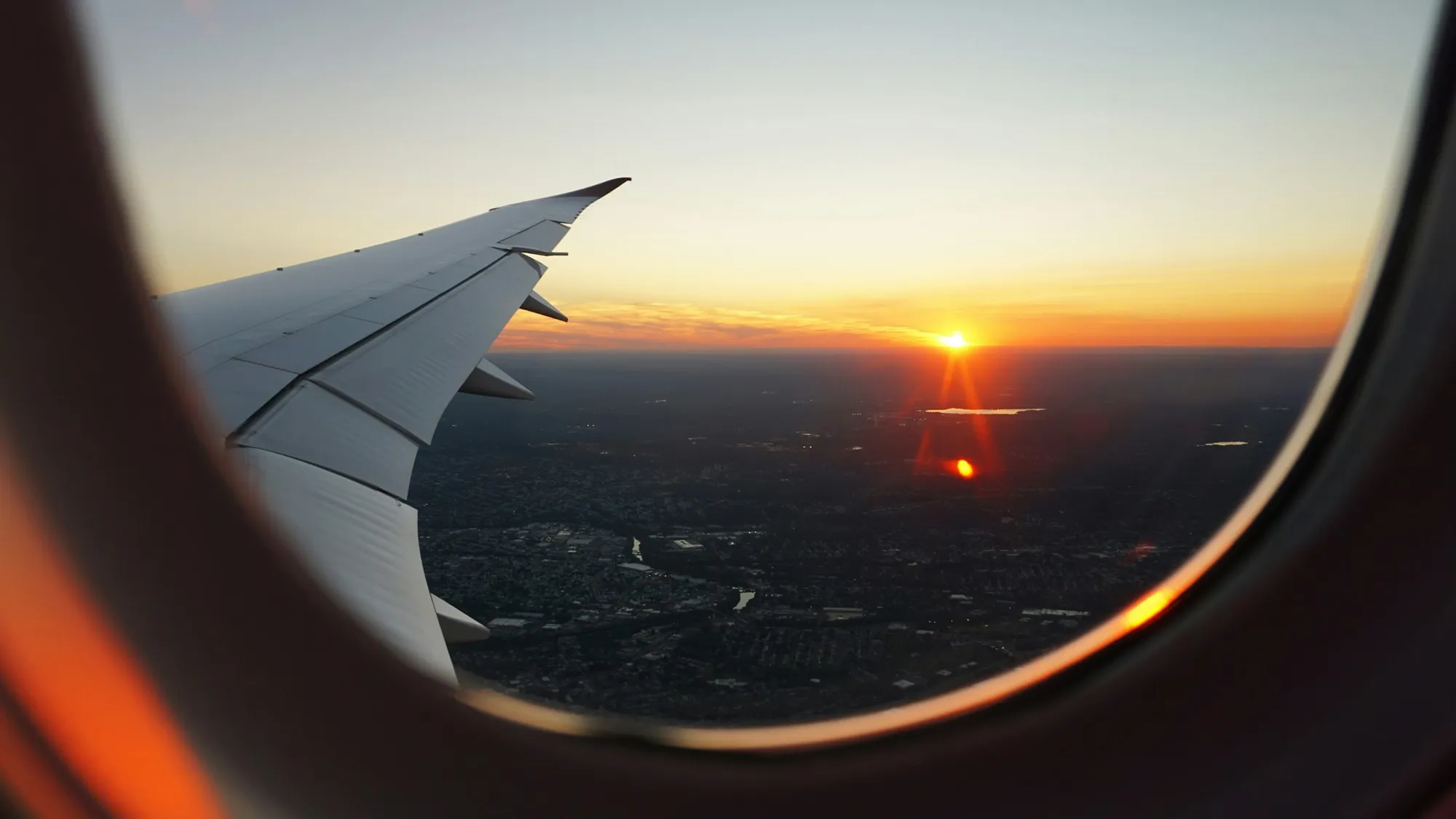
(Originally by Stas Mylek, October 1, 2016, CNC Software, Tolland, CT)
Contrary to popular belief, the cutting edges of cutting tools don’t actually produce chips. What happens is that the pressure of a rapidly spinning tool on a workpiece plasticizes part of the parent material, creating a shearing effect that forces the material to ride up the tool. The flute and tool geometries form the chip and force it away from the tool body until it breaks off and evacuates.
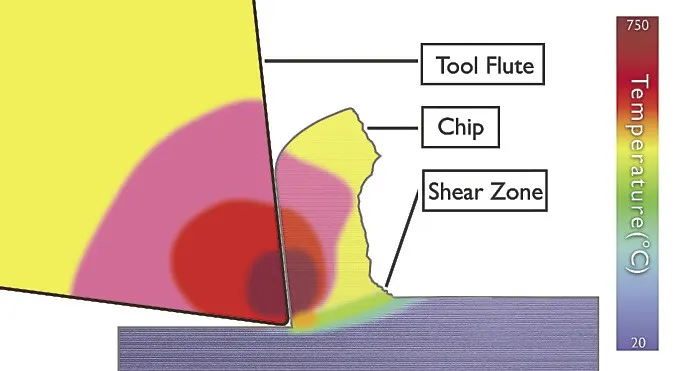
How can you make your CNC machining processes more effective?
One of the biggest takeaways is a heightened appreciation for the roles that machining parameter sand heat play when cutting metal. Therefore, it is generally a mistake to back off on the feeds and speeds to “protect” cutting tools and parts from heat damage.
Constant chip thickness is needed for keeping an optimal amount of heat in the chip and directing it away from the tool and workpiece. Heat is not always the enemy. Rather, it is an essential ingredient of the cutting process and should be carefully managed to create optimal material-removal conditions. Heat, and lots of it, is needed within the shear zone for efficient material removal. However, that heat should not be allowed to linger, lest it migrate into the part or the cutting tool. Instead, the heat must be removed via chip formation and evacuation.
Effective heat management is crucial for maintaining the integrity and longevity of both the tool and the workpiece. Properly managed heat helps in achieving smoother finishes, preventing tool wear, and ensuring dimensional accuracy. By maintaining constant chip thickness and optimal heat levels, the cutting process can be both efficient and precise.
Our temperature-controlled technology pulls all excess heat down through the part and away, maintaining the part, the vacuum fixture, and the bed of the gantry itself at a constant temperature of 68°F ± 3°F. This effectively minimizes thermal expansion and maintains dimensional accuracy for bore and pocket depth and overall size. This allows us to maintain a 53’ skin to 636” ± .048” vs. atypical ± .496” on a very hot day in a non-air-conditioned shop.
Adding Further Insights
In addition to temperature control, other innovations in CNC machining include the use of advanced materials and coatings for cutting tools, which can further enhance heat resistance and wear properties. For instance, titanium nitride (TiN) and aluminum titanium nitride (AlTiN) coatings are commonly used to improve tool life and performance by reducing friction and enhancing heat dissipation.
Moreover, implementing high-pressure coolant systems can significantly improve chip evacuation and cooling efficiency. These systems deliver coolant directly to the cutting zone at high pressures, which not only aids in chip removal but also helps in keeping the cutting tool and workpiece cool.
Another key aspect of effective CNC machining is the use of simulation software. By simulating the machining process, potential issues such as excessive heat generation, tool deflection, and chip evacuation problems can be identified and addressed before actual machining begins. This proactive approach can save time, reduce costs, and improve overall machining quality.
By combining advanced heat management techniques with innovative materials, coatings, and simulation tools, CNC machining processes can achieve higher efficiency, precision, and reliability. This holistic approach ensures that both the tools and workpieces are protected, and optimal machining conditions are maintained.
Conclusion
The intersection of advanced heat management techniques and innovative CNC machining practices offers a pathway to greater efficiency and precision in manufacturing. As we continue to explore and implement these advancements, the potential for achieving higher quality and more reliable machining outcomes grows, driving the industry forward.