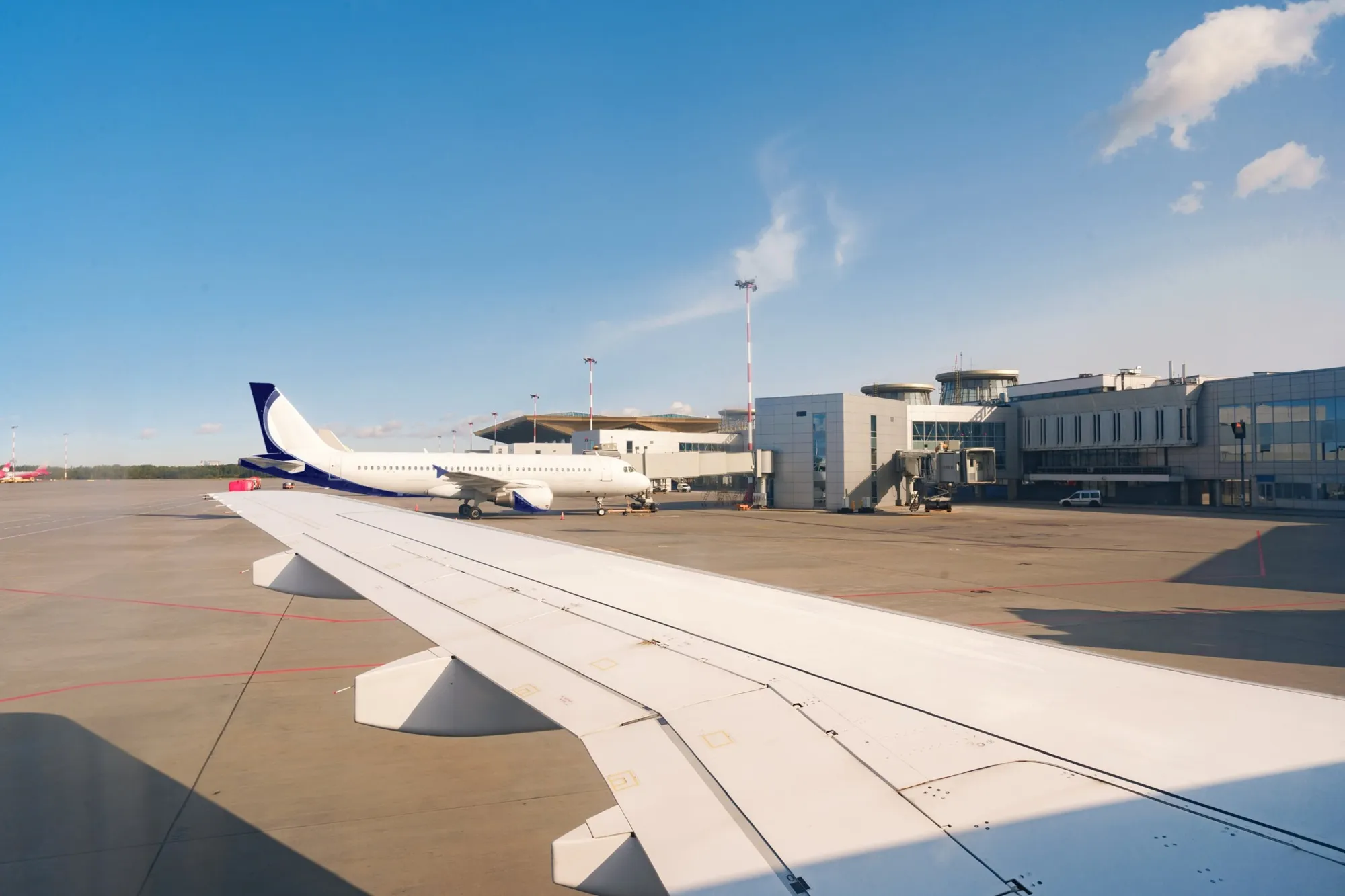
Green Wing Partners is a development stage Company founded to commercialize a proprietary technology for the manufacture of aircraft wing skins. The Company proposes to establish a wing skin production facility in centrally located Wichita, Kansas to supply wing skins.
Importing wing skins from the UK and Europe is expensive with built in 10 day shipping delays. Off-shore supply of these critical components, even from a reliable and experienced vendor, is necessarily less efficient than any on-shore supply. A U.S. supplier could add value in inventory management (JIT), reduced shipping and storage costs, and allow for running changes. Ongoing energy supply disruptions, climate deterioration, open ocean shipping bottlenecks, and increasing pandemic probabilities add incalculable future risks.
Green Wing proposes more than U.S. supply with dependable rail links to any US location. GWP has a proprietary and innovative wing machining process designed to produce high-precision, defect free wing skins, eliminate post-production rework, and reduce costs. A strategic partnership between any aircraft manufacturer and GWP could move this innovation from today’s “Proof Of Concept” stage to the production of accurate skins, at lower cost, with sustainable reliability, in a short period of time.
Under current wing skin machining processes, existing production rates necessarily generate high temperatures in the work piece. During a typical 8-hour machine cycle, wing skins absorb and accumulate this excess heat. The high Coefficient of Linear Thermal Expansion (CLTE) of aerospace aluminum alloys causes the material to expand. Expansion will shift the true position of machined-in surface contours. Accumulation of residual heat will also warp or bow the skin such that the skin fails inspection due to changes in surface contours. Substantial skin rework necessary to restore skins to specification is costly in labor, materials, and production delays.
GWP’s patented process continuously conducts excess heat energy from the skin to virtually eliminate dimensional expansion, warping, bowing and its associated downstream costs. GWP deploys several additional innovations to reduce machine cycle times and total machining costs. These include unique controls, instrumentation, and a semi-automated wing skin lift-rotate-replace robot.
We have designed, engineered, and fabricated a proof-of-concept prototype at 13:1 scale, including a dry machining vacuum work holding fixture. Testing of simulated sample parts confirm that the technology is both linear and scalable to a length of 15.925m. We anticipate the construction of a full-scale “proof of concept” demonstration vacuum fixture on a GWP-augmented gantry mill.
Our preliminary calculations forecast substantial manufacturing and life-cycle cost savings over existing production. At an anticipated post-pandemic production rate of up to seventy-five aircraft per month, savings could prove substantial. As a Wichita-based supplier, GWP can offer just-in-time delivery and can retain a just-in-case inventory accessible immediately if needed. Other benefits include savings in ocean shipping costs and reduced exposure to production delays and penalties. Compared to an offshore supplier, these advantages could achieve substantial cost reductions for main stream aircraft program lives.
In concert with our client, GWP would complete commercial development of our technology in three major phases. These will allow GWP (i) and (ii) goals.
(i). Verify GWP’s capability to machine skins at a constant, controlled temperature that obviates excess heat expansion, and
(ii). anticipated wing skin production from a single manufacturing “proof of concept”, demonstration cell.
- Construct a pre-production pilot to demonstrate, test, and refine an engineering prototype of a full scale production vacuum fixture. Machine and inspect sample, full-size wing skins for submission to client’s quality inspection.
- Launch a limited-production facility with a single machining cell to test, debug, and refine the process. Deliver limited number of skins to the client (using vendors for peening and coating) for assembly into client’s production aircraft.
- Ramp up production to meet client’s monthly requirements for dry machined, laser peened, chromate coated, and painted to 15.849 m (624”) skins
Our five-year, financial forecast model estimates expenses to accomplish the four-phase plan described above and develop GWP into a going concern. Based on our assumptions, the model predicts that GWP can grow rapidly in financial strength at prices attractive to our clients.