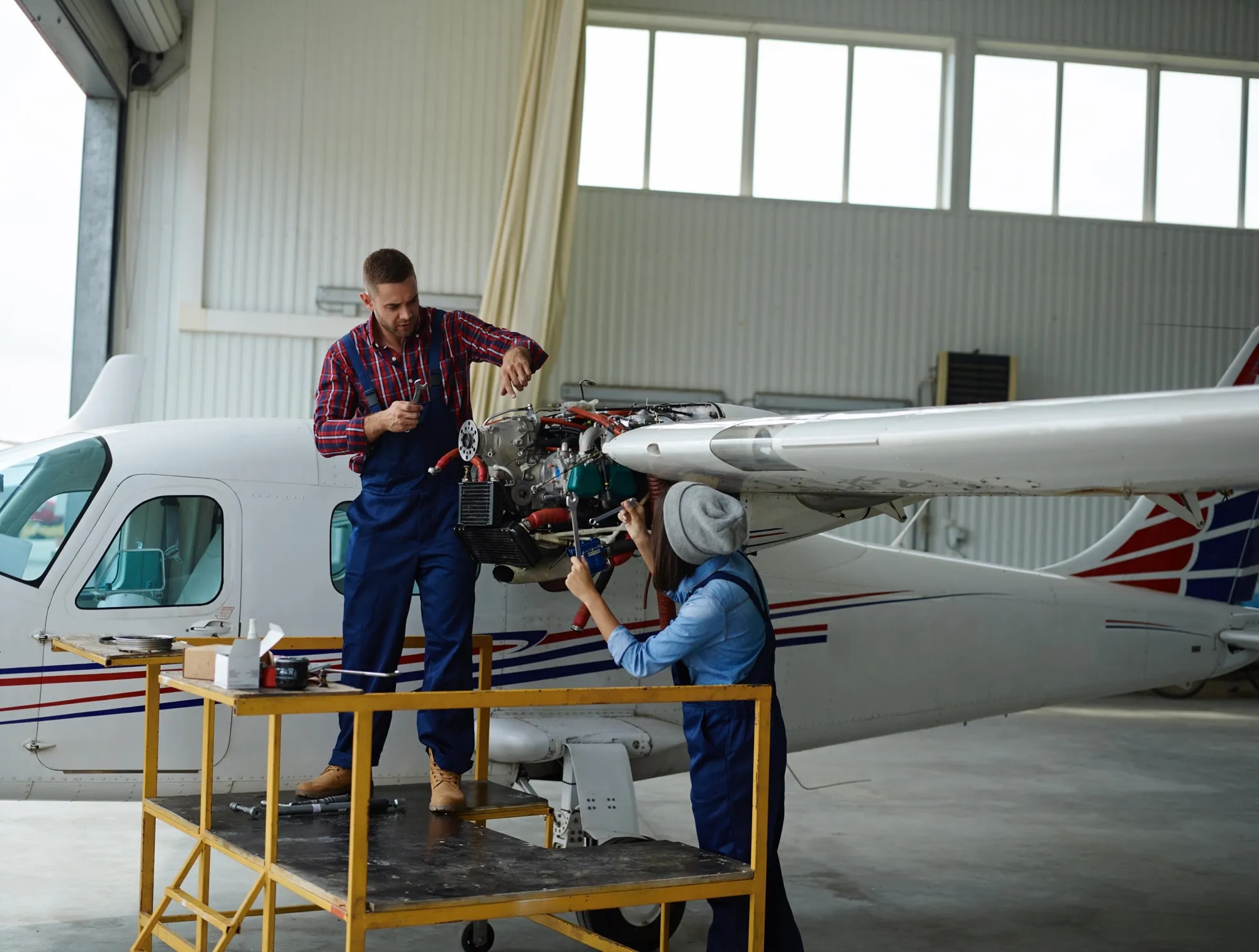
When I worked at Boeing, I was a CNC Maintenance Tech. It was summer time and many workers were going on vacation so management asked for volunteers to cover all buildings all shifts. I volunteered and was assigned to cover Building #6 dayshift where wing skins were manufactured. I came to work as usual and listened to the brief safety meeting, was given my tasks to begin work. As I riding my work tricycle out to the gantry mill, I heard this loud noise coming from a different machine nearby.
When I arrived, the noise was deafening so I put on ear plugs and ear muffs. As I walked up, I saw a very small part which I estimated to be about 45 feet long and 3 feet wide attached at the bottom much like you would hold a tuning fork from the bottom.
This part was vibrating so intensely, that it was shaking the fixture holding the part, the machine frame, the “in ground” concrete foundation which is 8 feet wide 8 feet deep by about 75 feet long. When I stood about 10 feet away from the machine base, I could feel the vibrations shaking the soles of my feet though my heavy work boots and 2 sets of insoles. This was worst machining I ever saw in my life. I said to myself there has to be a better way. I did my assigned work and finished both of my shifts that weekend.
I normally worked second shift so on Monday morning, I was reading through my mail that I did not get to that weekend. I was interested in machining skills for my job. I picked up the latest issue of “Tooling and Production” and was skimming through when I started reading an article about polymer enhanced concrete and its vibration damping. When I learned about the amazing damping attributes, I started thinking about the worst machining I witnessed 2 days prior. My Dad was a carpenter before he decided to start farming so I had poured concrete in a dozen different projects on the very large farm with my Dad and brothers.
In that Eureka moment, I realized I had all the basic skill sets to design, engineer, fabricate, test and finish machine [actually grind smooth flat surfaces] for a vacuum a fixture base plate. I designed in large diameter piping for highly efficient vacuum pumping. I have worked on 3 very large vacuum heat treat furnaces for titanium jet engine frames so I know how to design that portion. I could fabricate [saw, assemble and align] the precise engineered wood forms to tight tolerances for casting on a simple but accurate table saw. I also designed the matching aluminum cooling plate with integrated vacuum ports to match the concrete ports below and the rubber vacuum seal groove design for optimum effect. I could also precisely bend steel and copper tubing from my days when I worked on construction as an Instrument tech.
The only portion I was missing was an optimum concrete mix with admixtures to greatly increase stiffness, compressive strength, inherent natural porosity to essentially zero [leak tight] and design the mix for a very high resistance to heat flow or essentially an insulator.
I started researching standard admixtures, mix design, and reached out to a few concrete engineers asking how to design my mix. With the help of 3 different engineers, I was offered samples of admixtures by the companies they worked for. I started worked in my double garage with a small concrete mixer, a standard carpenter’s table saw and all my hand tools.
With a very systematic “design of experiments” approach that I had learned about from my research, I worked at creating my mix designs, optimizing the mixing sequence, weights not volumes and started creating 24” by 2” by 4” ingot samples to test. I also incorporated post tensioning for added strength. Within 6 months I could pour any shape I desired with embedded steel threaded inserts set inside of epoxy resin filled pockets so I could bolt to or through my castings. The last step was to hide the concrete look of the casting with standard garage floor epoxy resin based paint so it looked like a typical cast iron casting. I started by adding on [extending] the “ways” [linear liners] of my Bridgeport knee mill and my 2 grinder bases. I could now machine and grind bigger longer parts as the moveable portions could now travel 2X as far.
When that worked, I bought a much bigger scrap, cast iron casting 16 feet long, 6000# for $600 and started machining off small portions as needed, adding roller ball linear guides along with rack & pinion drives. I painted this 50 year old casting blue. It is the same blue casting you see in the pictures I sent you. That was the X axis that carried the temperature controlled vacuum fixture on top of dual 1” thick steel plates which I machined by hand hanging off of a small steel gantry hoist on top of my newly enhanced Bridgeport knee mill in the garage. The plates are annealed, straight ground and bolted together so they can ride on the linear guides. The blue casting itself was mounted on top of a custom poured, high strength, and post tensioned concrete casting 24” high by 48” wide and 20’ long. I formed up, poured and trowelled down myself. I used an old, $100 fork lift nobody wanted and fixed it up so worked. I also bought a used 3 ton rated engine hoist nobody wanted to carry the other end of this 6000# casting to lift it up on top of the 24 inch high concrete foundation.
I hired and sat down with a local CAD jockey whose dad owned a machine shop for about 3 months. I sketched out portions of the rest of the machine design, did all the force and moment calculations on the fly. I had him draft it up in CAD so we had very accurate dimensions on all parts. I could then saw, cut, drill and bolt up the steel frame. I also built up two very complex designed but simple to look at 3 meter vertical columns which sat on two 8 foot long polymer beams. These held the moveable Y and Z axis.
Bye the way, I bought a used hydraulic sheet metal shear and a used 10' long sheet metal brake both for $1800 and sold the shear back for $900 after I was done. I used over 100 4' by 8' sheets of .032" galvanized sheets and well over 40,000 rivets to cover up the frame. The mill was 28' long 18' feet high and 14' feet deep along the horizontal Z axis. I ran 900 feet of 1/2" copper tubing throughout the steel frame to keep the mill at 68F for dimensional stability
You have the rest of the story from here down.
Thinking about it I forgot to mention a small issue. I built an entire machine tool around this tiny fixture. I had worked for an incredible # of months, over about 48 months, 12 hours a day, 7 days a week to build the machine mostly from scratch. I purchased the motors, rack & pinion, gear boxes, ball screws and the control, the spindle the spindle drive and spindle cooler but the frame, the polymer concrete columns and beams were my own unique design, mix design, fabrication and mechanical alignment etc.
By the time I started building the vacuum fixture I was just exhausted from fatigue; physically, mentally and emotionally. I was just glad the vacuum fixture worked as I had designed.
Here are a few pictures of the machine tool I built and took pictures of along the way. The X axis sitting on top of the blue casting had 10' of travel horizontally. The vertical Y axis has 8 feet of travel up and down and the short Z axis with the spindle in towards the part to be milled had 29 inches of travel.
Once the mill is assembled, aligned and the controls moved the motors which move the axis, its time to test. So you start with tooling foam which is hard enough that it replicates the cut surfaces exactly. You can measure the cut features after to see how far off the mill is. As long as the mill is repeatable, then you can laser compensate for inaccuracy in all axis. Then re-cut foam again to verify the laser comp values are correct.
Then it’s time to try a soft material like aluminum to see if it is rigid and repeats and then measure your "as milled" part and then you can comp the program with offsets to dial in the features for accuracy.
If you look at the North End Picture, you can see the foam block we will milling during initial testing and dialing it in.
If you look at the ....0564 picture you can see one of the sample test pieces we were milling on with sample test pockets milled out.
If you look at ....0564 picture and zoom in on the lower left corner you can see more foam blocks sitting against the wall on the floor. The one small scrap piece of aluminum was the next piece to be milled out with one large pocket. I seem to recall it was 24 by 24 by 1" thick. We milled one large pocket 22 by 22 by .940 or just shy of 1 inch deep for a very thin layer left on the bottom which was straight after we examined it. Just imagine the part in ...0564 picture with one large pocket instead of 4 pockets.
We then went on to mill out a 48" by 48" by 1 inch thick scrape plate with a pocket of 44" by 44" by the same 0.940" deep. It came off with a thin 0.060" face left over and it was also very straight; not warped which is what I wanted to prove. This is extremely hard to do on any mill with dry machining as the heat builds up. in 2 of the pictures, I used a tiny ultrasonic mist of lubrication to prevent built up edge on the flutes of the end mill. If you do not address this, the tool loads up and eventually breaks as it if being pushed sideways through the material. I know as I broke a tool before using the mist to keep it clean so it cuts optimally.
Since this process works down to .060" it will be much easier to hold a wing skin with .0375" edge straight as there is so much more material. The thinner the material is, the easier it is to warp, twist and bow. I used the 0.060" as a worst case scenario. This 0.060" plate is 6.25 times thinner than 0.375" skin edge right at the wing tip.
I just need to make sure I have a big enough chiller to cool the water to pull all the residual heat down though the skin as fast as the heat is created by the 100 hp spindle with up to a 12" diameter face mill.; lots of heat to transfer but I have 8 hours to do it.
We ran ordinary tap water through the copper tubing in the fixture that was about 52 to 54F for the cooling of the fixture so it definitely was cool to the touch. We did this in the middle of summer with about a 75 to 80 F degree day. The water flow was whatever flow we could push through a 1/2" copper tube with about 30-40 psi source pressure. I was not really worried about documenting all the flows and temperatures etc. As you said, I knew intuitively this would work for a much thicker skin even near the edge and next to the wing tip.